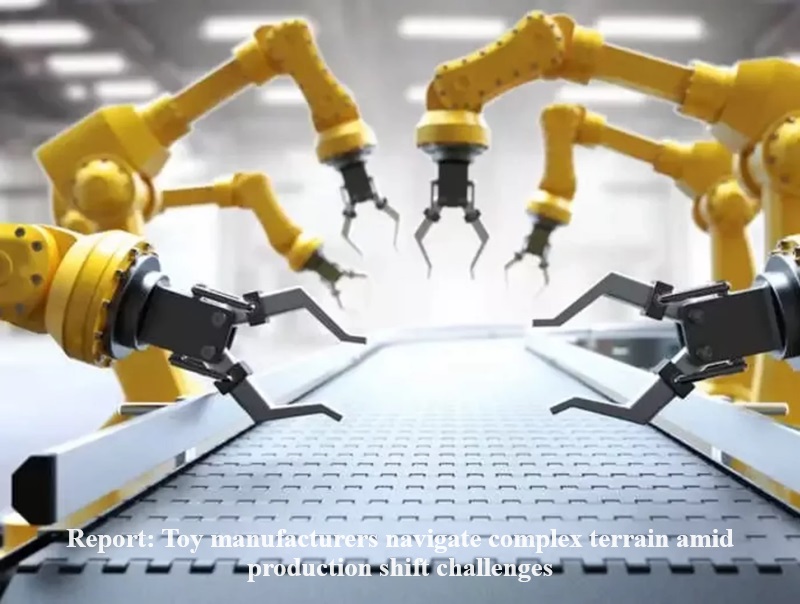
Toy manufacturers are contending with the complexities of relocating production away from China as rising costs and global disruptions reshape supply chain dynamics, according to a Reuters report. The Boston Consulting Group underscored the formidable challenges faced by toy makers in a study, emphasizing that such a transition is no straightforward feat.
Six years ago, Hasbro initiated a move towards diversification by collaborating with Indian supplier Aequs for subcontracting toy manufacturing. Rohit Hegde, Aequs’ head of consumer verticals, shared, “They said if you can get into toy manufacturing, now we’re looking to shift millions of dollars worth of product from China to India.” Aequs now manufactures various toys for Hasbro and Spin Master in India. However, Hegde acknowledged the efficiency gap, stating, “We don’t have the port facilities (in India) that China does. They have been doing this for the last 30 years; their efficiency levels are much better than ours.”
Despite the challenges, toy manufacturers recognize the risks of heavy reliance on China, especially evident during the COVID-19 pandemic when Chinese ports faced operational difficulties. Escalating labor costs in China have been prompting various industries to explore geographical diversification. Yet, even as other sectors successfully shift production, the toy industry finds it challenging to follow suit.
As of the first seven months of 2023, mainland China still produced 79 percent of toys sold in the United States and Europe, a slight decrease from 82 percent in 2019. Chris Rogers from S&P Global Market Intelligence highlighted, “Is it easy to re-shore away from mainland China? No, it isn’t. That goes double for toys.” The toy industry faces added complexities due to its highly seasonal nature and stringent safety and sourcing requirements.
The study revealed that, despite rising wages in China leading to higher toy prices, manufacturers are compelled to consider alternative production centers to maintain cost-effectiveness. While China’s minimum wage varies, India offers unskilled and semi-skilled workers at a monthly rate of 9,000 to 15,000 Indian rupees. However, transitioning to other countries involves a significant time investment, ranging from 18 months to three years, depending on the manufacturing process.
Leading toy manufacturers, including Hasbro and Mattel, have recognized the need to de-risk their dependence on China. Spiraling Chinese wages contributed to an 8 percent price increase in the UK in the first half of 2022. With the potential for changes in US duties on Chinese toys, manufacturers are exploring more cost-effective production centers. Nic Aldridge, managing director at Bandai UK, emphasized the industry’s focus on de-risking China, stating, “We are all looking at de-risking China. Raw materials costs have gone up a lot in China; we’re looking for places where we could get a more reasonable cost.” Bandai is exploring additional manufacturing locations such as India and Thailand, recognizing the importance of a diversified supply chain.
Post Your Comments